We have previously covered on what are the types of businesses that will be affected by the Mandatory Food Waste Segregation requirements. Over here at Thriving Weeds, we suggest for affected businesses to first think of their food waste in the categories shown below. We will build onto the previous Case Study of Shopping Malls in this sharing on the different types of food treatment machines, and suggest what businesses can do in the way forward.
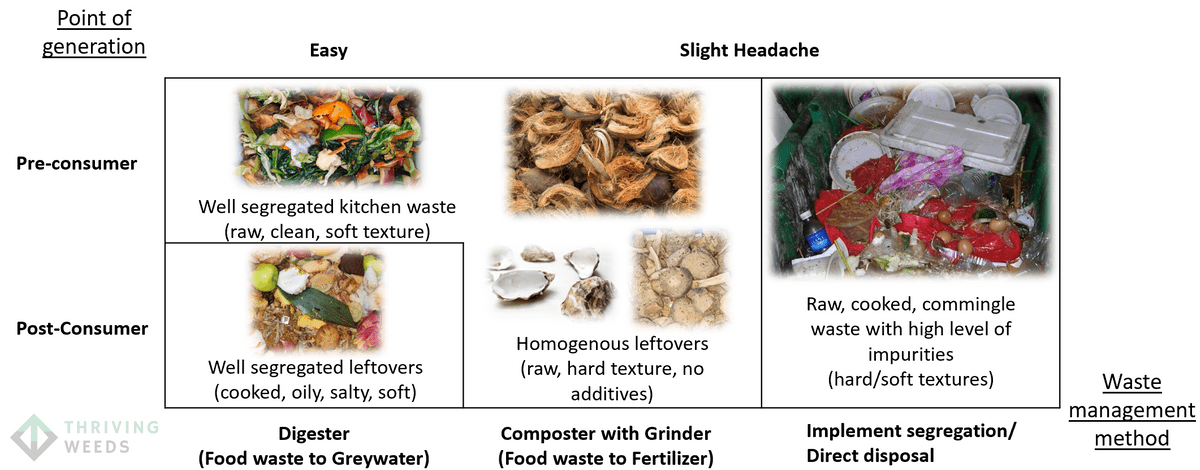
Figure 1: Top-level view on the common waste found in malls and the potential solutions to explore
Steps to Achieve Food Waste Segregation
1. Segregate between Pre-Consumer and Post-Consumer food waste.
2. F&B Shops can introduce 3/4-bin system
- Soft Pre-consumer kitchen waste;
- Recyclable packaging waste;
- Contaminated packaging waste;
- Hard Pre-Consumer kitchen + Post-Consumer food waste (bones etc) (May be optional)
3. Malls can deploy Grinders (depending on management outcome) + Dryer/ Digester/ Composter in bin centres.
4. Packaging waste
Understanding Digester / Composter / Dryer
Food waste can be processed using various methods, each with its own advantages and limitations. Some common ways of processing food waste include:
1. Digester: This involves breaking down organic matter in food waste using microorganisms. Greywater slurry is the output that can be diverted into the sewage system or converted into fertilizers. The on-site food waste digesters are mainly aerobic digesters (requires oxygen) which do not emit foul smell. A digester is suitable for on-site food waste treatment system for post-consumer food waste. The operating temperature for what is available now in the market is about 40°C. Energy consumption will not be as high as the composter nor the dryer.
2. Composter: Food waste is broken down into nutrient-rich soil through microbial activity. Composting can be accelerated using machines to speed up the biodegradation process. The resulting compost can be used as a natural fertilizer for plants. Composting is suitable for factories, pre-consumer food waste, and ground hard food waste which is homogenous. The operating temperature for technology available in the market now ranges from 40°C to 80°C. Usually, if the electricity consumption increases with increasing operating temperature. Remember to check with your vendor!
3. Dryer: In this process, liquids are extracted from the food waste and passed off as vapors or discharged as greywater. The remaining dry food waste can be compacted and pelletized into Refuse Derived Fuel (RDF) that can be used for heat and power generation when sent to the Waste-to-Energy plant. This approach is useful in reducing mass, storing waste for a longer period, and can significantly reduce waste tonnage figures.
Note: We have excluded the option of dryer in Figure 1. We believe the costs will outweigh the gains from this investment. Based on our experience:
- Drying food waste with high moisture content is most likely to be a slow process (e.g. drying clothes in dryer) to be done in batches.
- Drying requires high energy.
- Dried waste will still have to be removed by waste collector for incineration.
Each of these methods offers an opportunity to reduce food waste and recycle valuable resources. Choosing the right method depends on the type of waste, the quantity of waste generated, and the desired end-use of the recycled material.
The most suitable technology would depend on a balance between many different factors.
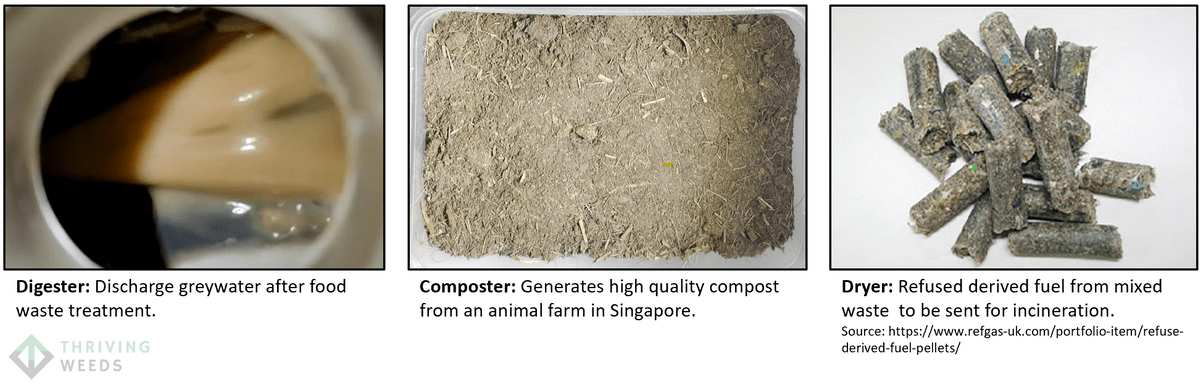
Figure 2. Images of food waste treatment system discharge
Speak or email us at Thriving Weeds for an assessment now